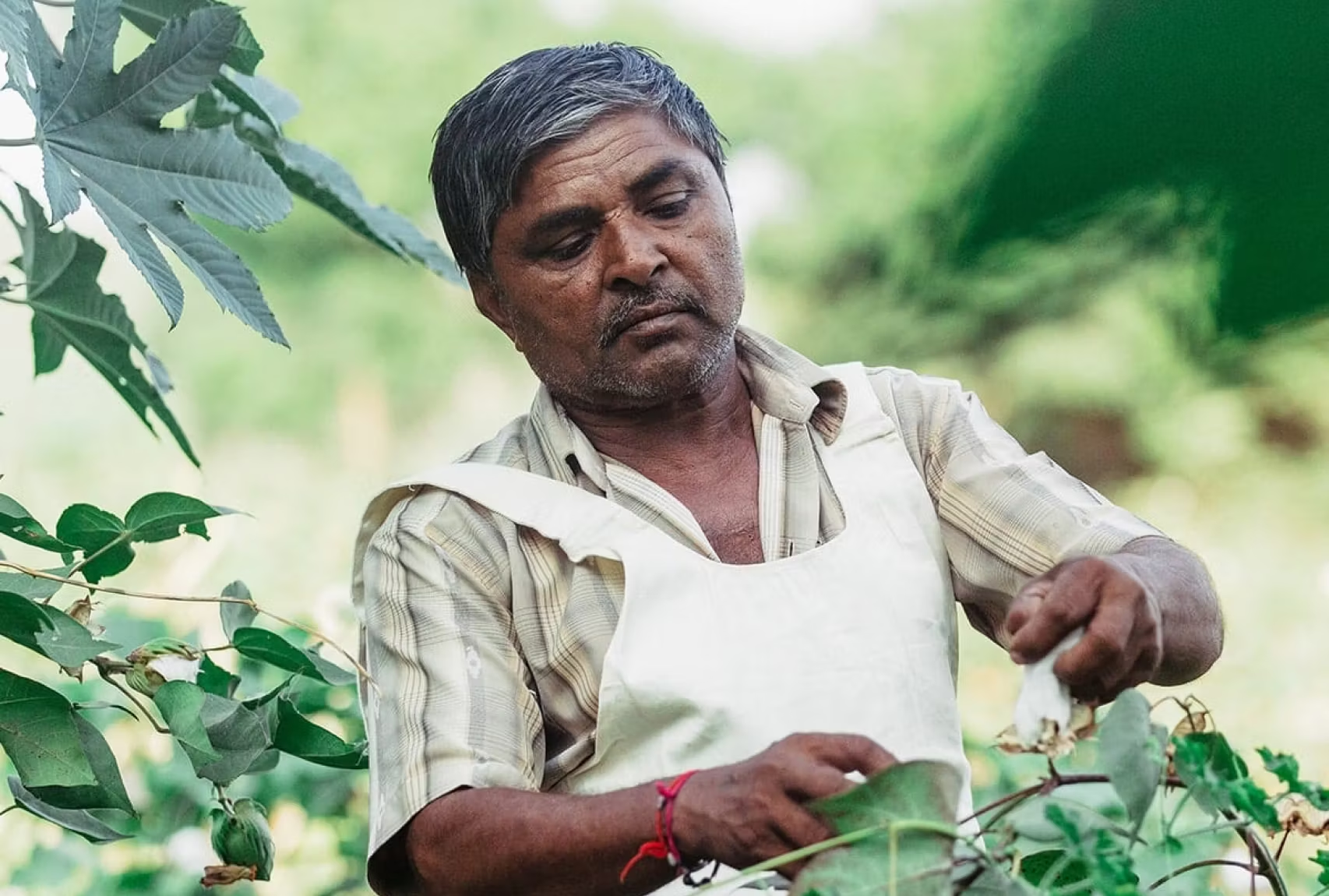
Step 1
De teelt
Ons biologische katoen wordt geteeld volgens de richtlijnen van de ecologische landbouw. Langetermijnstudies over biologische bedrijven hebben aangetoond dat biologische landbouw 18 procent minder broeikasgassen uitstoot dan andere landbouwsystemen.* *Bron: Textile exchange (2021) Material summary on Organic, In-Conversion Cotton.
Als alternatief gebruiken de boeren en boerinnen mest en compost voor de bemesting, wat de vruchtbaarheid van de bodem en zijn resistentie tegen erosie steeds verbetert. Een jaarlijkse vruchtwisseling behoort eveneens tot de verplichtingen. Door de rotatie van katoen en andere gewassen worden schadelijke insecten en ziektes op een natuurlijke manier verhinderd en wordt de bodem verder verrijkt.
Door zijn hoge humuspercentage is deze grond niet alleen vruchtbaarder, maar kan hij ook meer water en atmosferische CO2 opslaan.
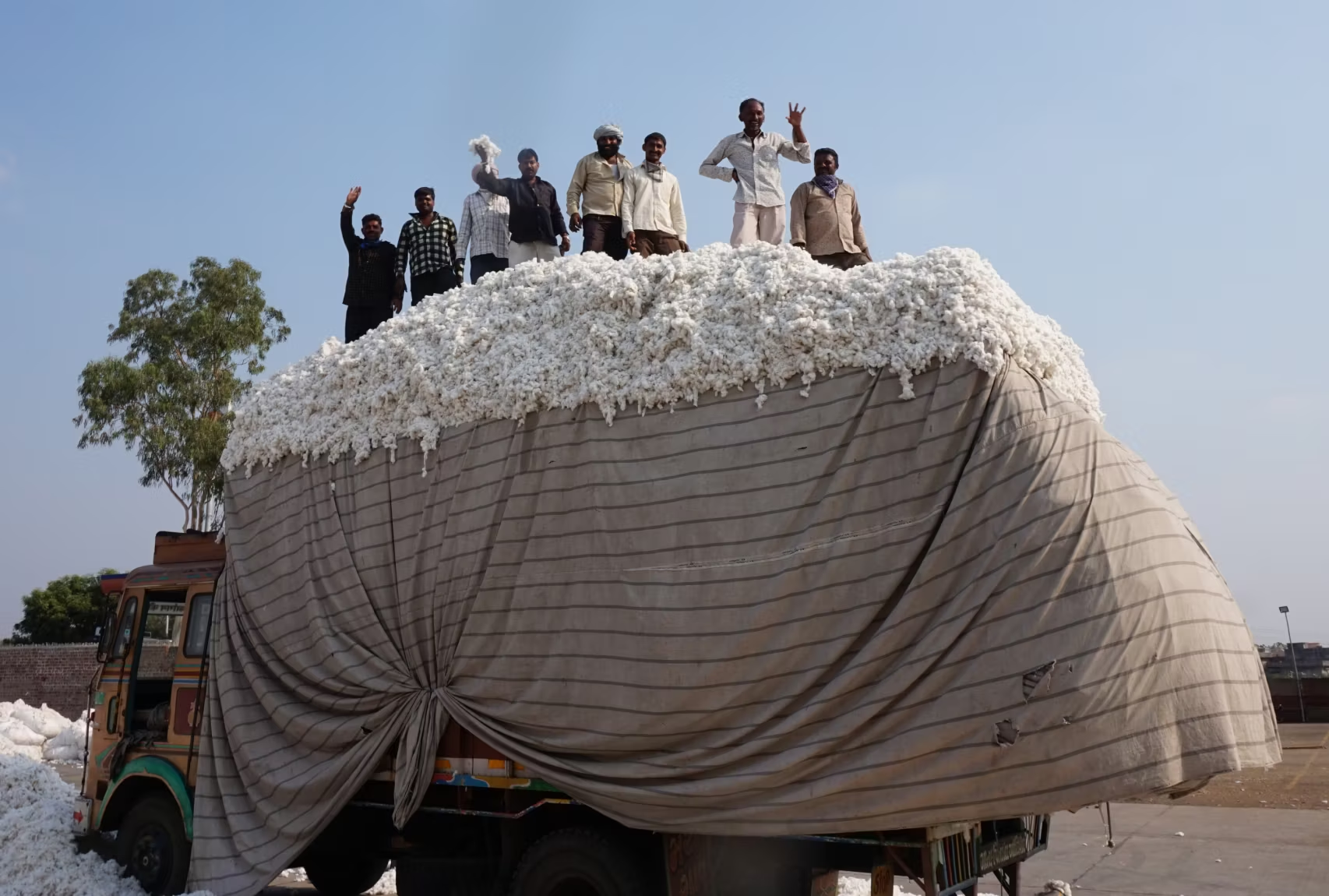
Step 2
De oogst
Biologisch katoen wordt een keer per jaar geoogst. Anders dan bij de traditionele teelt van katoen zijn chemische ontbladeringsmiddelen, die gebruikt worden om de machinale oogst te vereenvoudigen, hier verboden.
Om de overstap van traditioneel naar biologisch katoen te vergemakkelijken hebben we in april 2018 de ARMEDANGELS Organic Farmers Association opgericht. Die ondersteunt momenteel meer dan 500 kleinschalige boer(inn)en in India bij het driejarige omschakelingsproces.
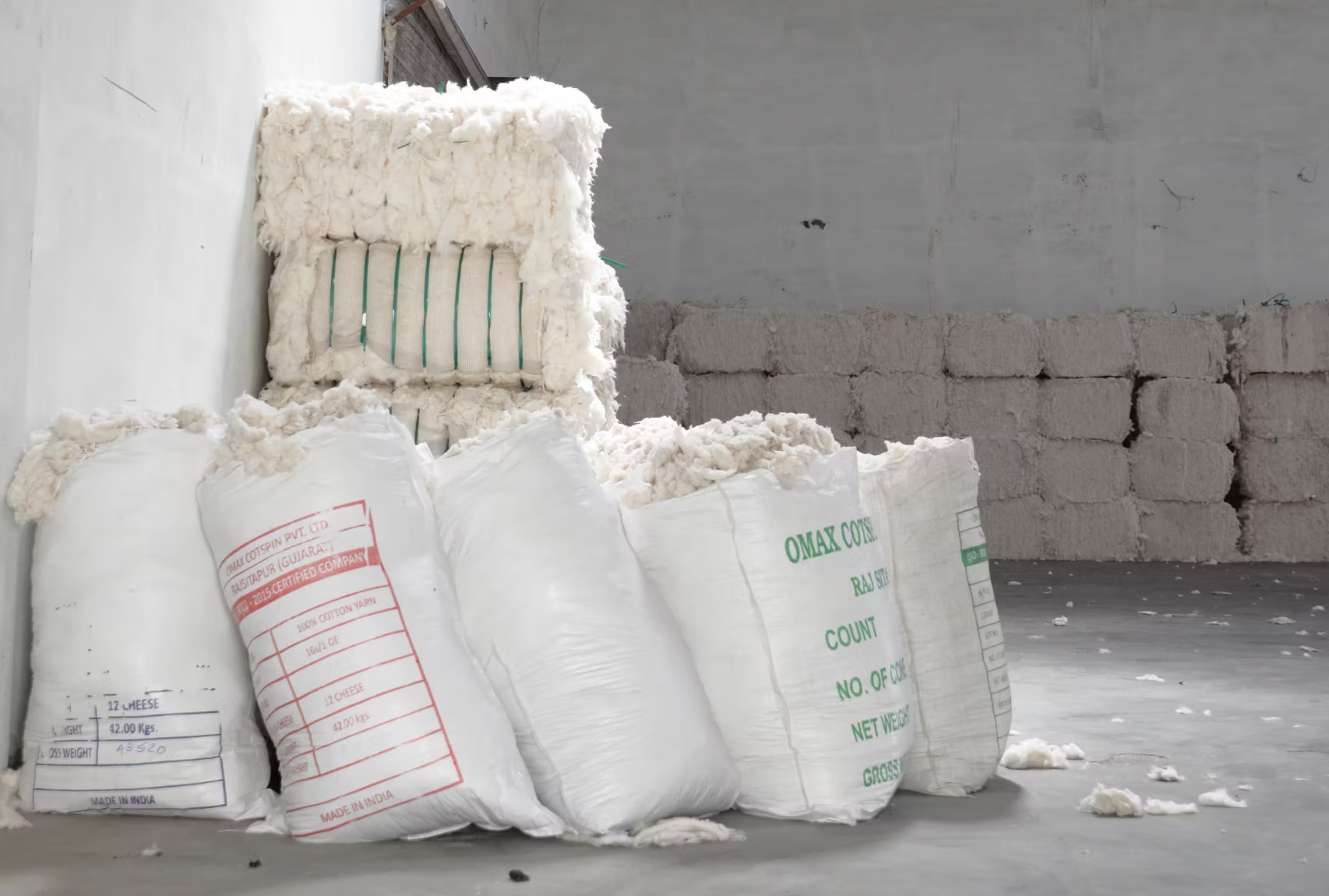
Step 3
De vezel
Meteen na de oogst wordt het ruwe katoen naar speciale verwerkingsbedrijven gebracht om de katoenvezels van het zaad te scheiden. Dat gebeurt volledig automatisch met behulp van een speciale ontkorrelmachine, de cotton gin.
Het volledige ontkorrelproces wordt streng gecontroleerd om het katoen gescheiden te houden op basis van kwaliteit en teeltwijze (biologisch of traditioneel).
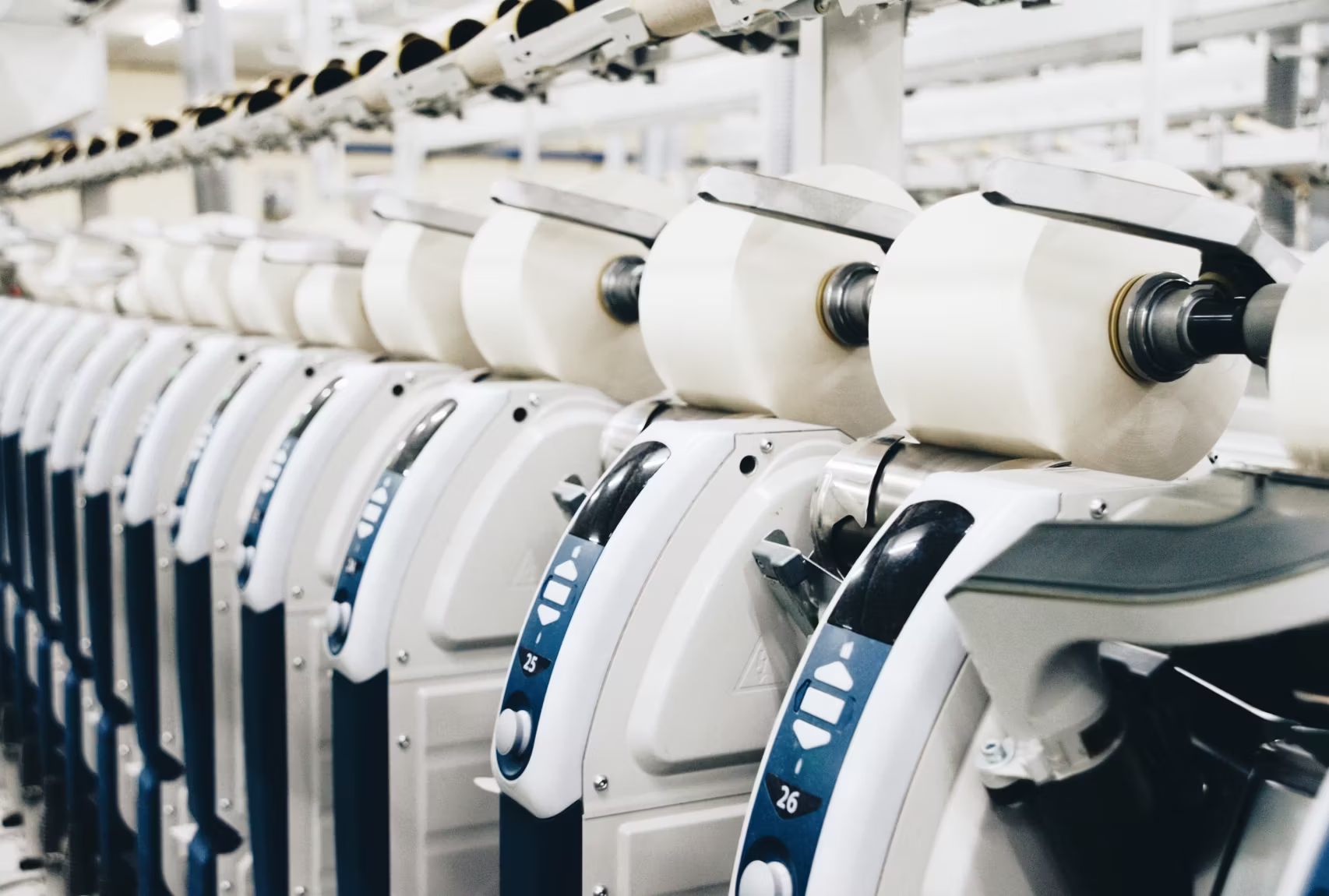
Step 4
Het garen
Tijdens het spinnen worden aparte korte vezels en vezelbundels gerekt en in elkaar gedraaid, zodat ze samen een gelijkmatige draad of garen vormen. Vroeger was dat nog een arbeidsintensief proces met de hand en het spinnenwiel, maar nu gebeurt het doorgaans volledig automatisch.
De volledig gesponnen draad wordt vervolgens in strengen of op een klos gewikkeld voor verdere verwerking.
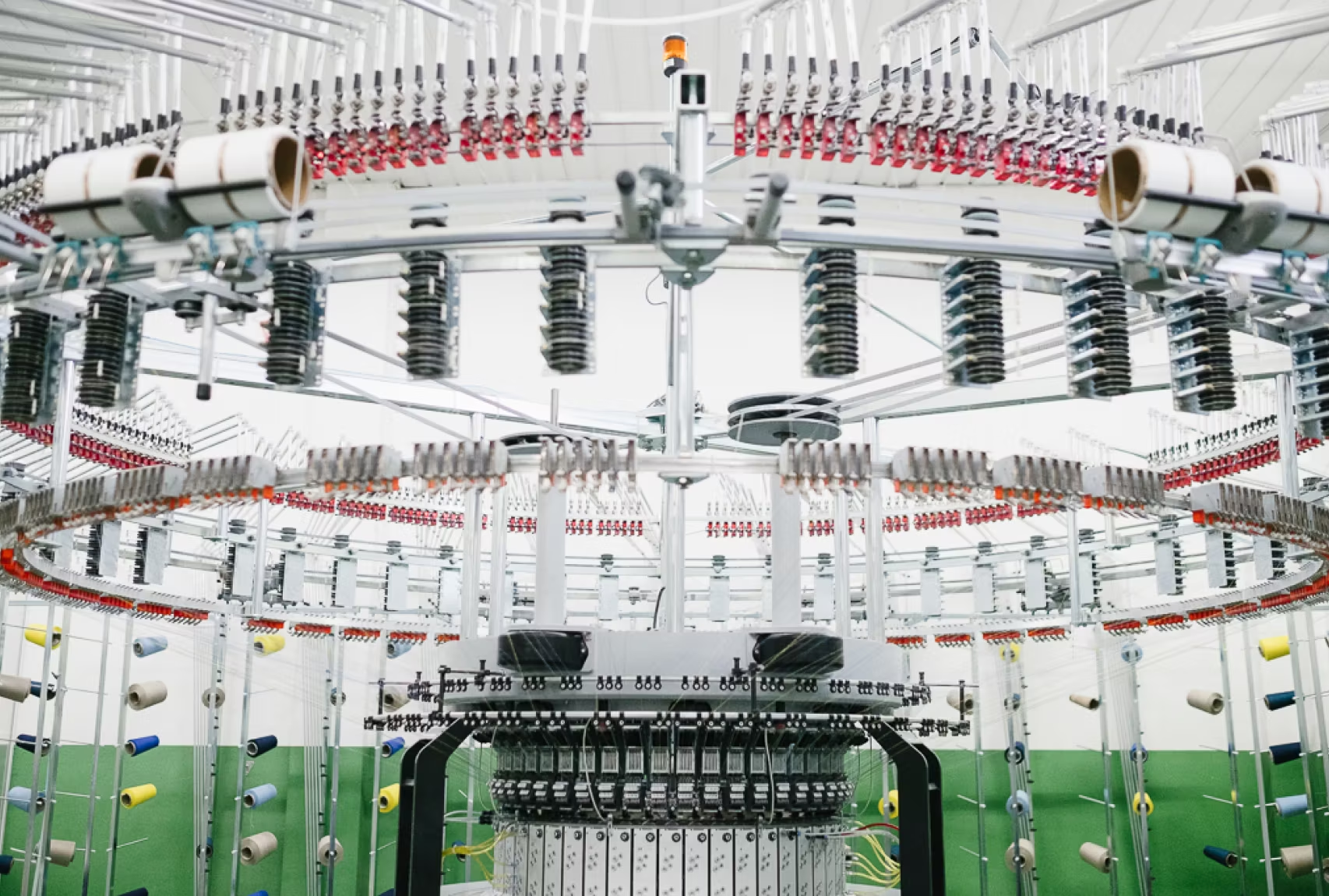
Step 5
Breien
Voor onze T-shirts van biologisch katoen wordt een single-jerseystof gemaakt. In tegenstelling tot weefsels waarbij twee draadsystemen gekruist worden, gaat het hier om een gebreide stof waarbij draadlussen met elkaar worden verbonden.
Dit proces verloopt volledig automatisch met grote rondbreimachines die van veel aparte draden een jerseystof breien.
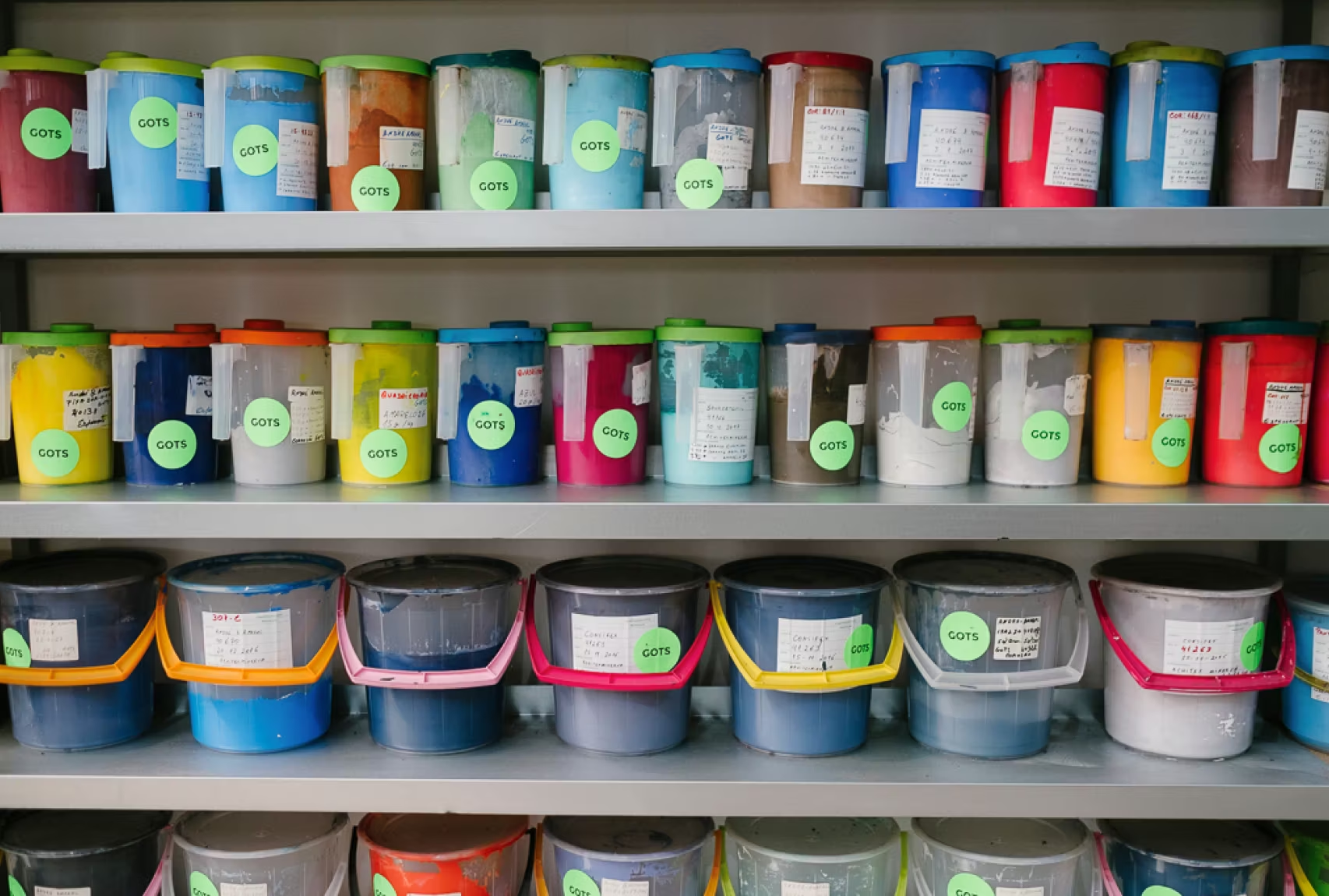
Step 6
Verven + veredelen
Bij het verven van textiel worden in traditionele fabrieken veel schadelijke chemicaliën gebruikt en gezondheidsrisico's gecreëerd. Schadelijke stoffen in het textiel kunnen bij het dragen van een T-shirts loskomen van de vezels, in het lichaam binnendringen en allergische reacties of aandoeningen aan het immuunsysteem veroorzaken.
Bij het verven van textiel worden in traditionele fabrieken veel chemische producten gebruikt en gezondheidsrisico's gecreëerd. Schadelijke stoffen in het textiel kunnen bij het dragen van een T-shirts loskomen van de vezels, in het lichaam binnendringen en allergische reacties of aandoeningen aan het immuunsysteem veroorzaken.
Als alternatief kunnen kleurmiddelen gebruikt worden die door de Global Organic Textile Standard worden toegelaten. Die kleurstoffen en chemische stoffen zijn allemaal gecontroleerd op gifstoffen. Dankzij moderne filtersystemen wordt ook het afvalwater niet vervuild.
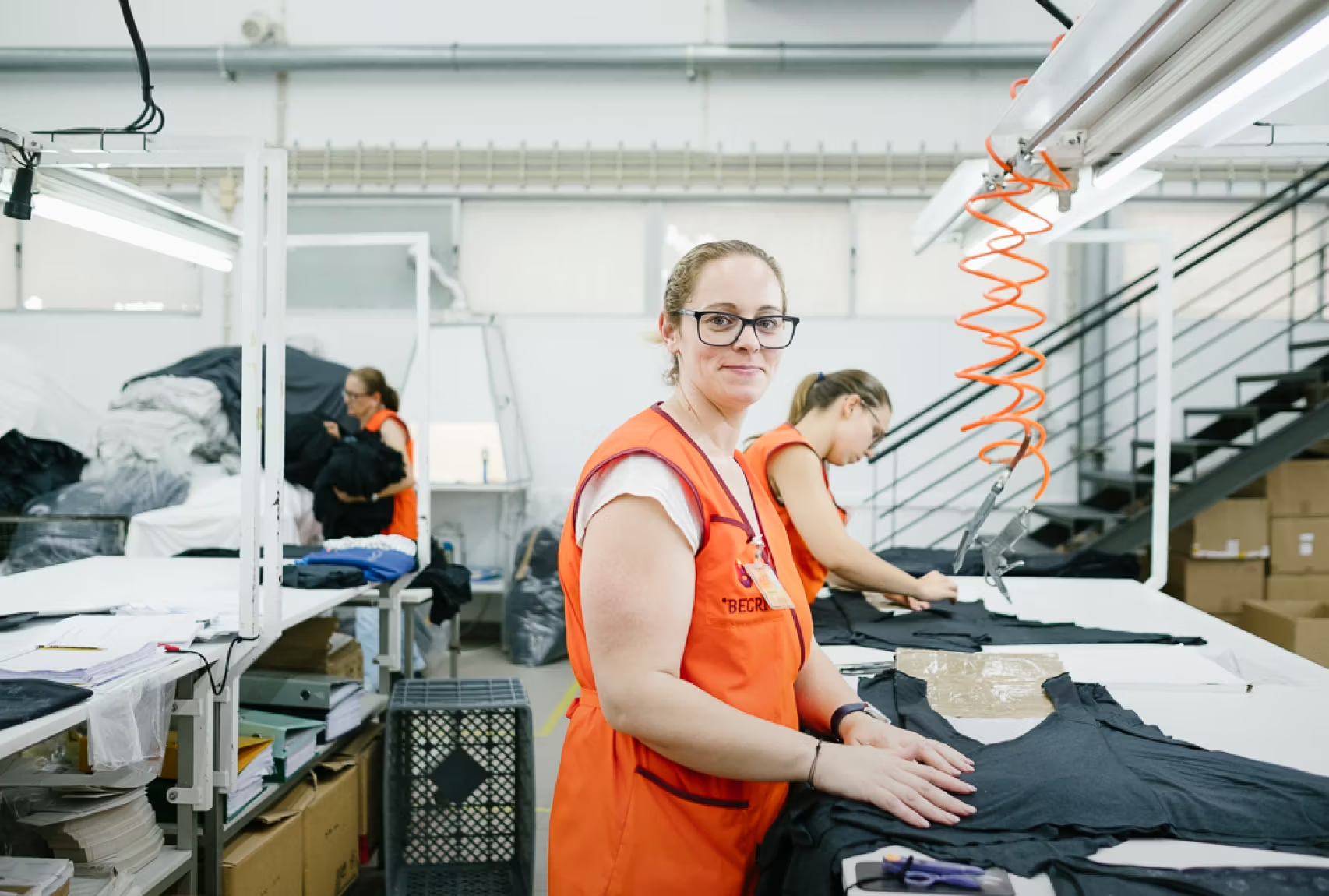
Step 7
De confectie
De confectie omvat het knippen, naaien en afwerken van een kledingstuk. Hier wordt een 2-dimensionale stof veranderd in een 3-dimensionaal kledingstuk.
Voor ons T-shirt van biologisch katoen JAAMES vindt de confectie bij onze gecertificeerde partners in Portugal plaats. Zoals bij alle partners eisen we ook hier: eerlijke lonen voor de medewerk(st)ers in de naaifabrieken, geen kinderarbeid, meer veiligheid op de werkvloer en minder overuren.